Exploring the Versatility of Ultem in 3D Printing
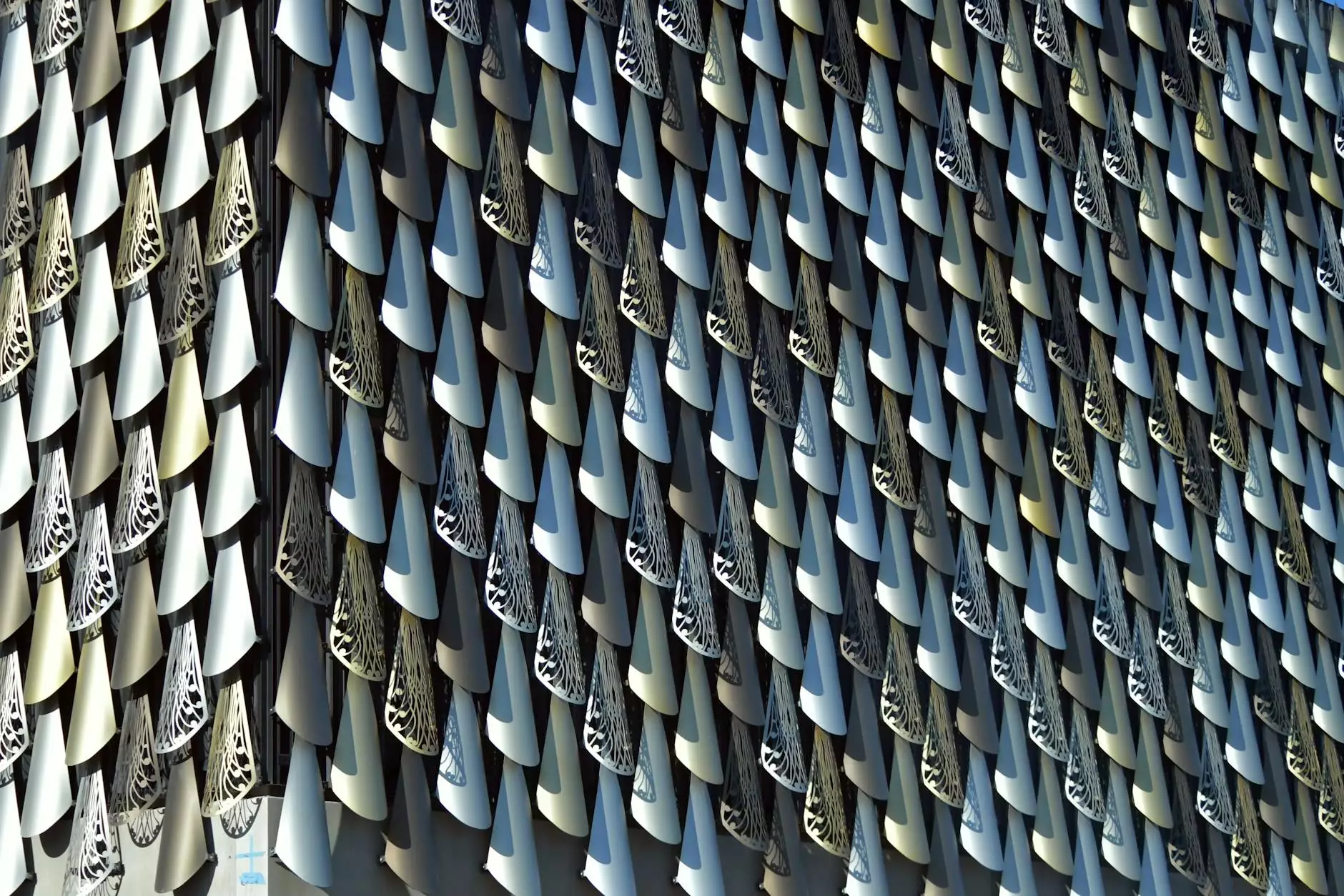
The world of 3D printing has transformed rapidly over the last few years, marking a significant shift in how industries approach manufacturing and design. Among the materials leading the charge in this revolution is Ultem, a remarkable thermoplastic that has become synonymous with high-performance applications. This article delves deep into the characteristics, advantages, and diverse applications of Ultem in 3D printing, providing insights for businesses looking to leverage this technology.
What is Ultem? Understanding Polyetherimide (PEI)
Ultem is the brand name for a group of high-performance thermoplastic polyetherimide (PEI) materials developed by SABIC. Known for its excellent mechanical properties and thermal stability, Ultem is a polymer that can withstand harsh environments while maintaining its structural integrity. What sets Ultem apart from other materials is its ability to perform under high temperatures and loads, making it a top choice in multiple engineering sectors.
Characteristics of Ultem
- High Thermal Stability:Ultem can maintain its shape and properties at temperatures exceeding 200°C (392°F), making it ideal for applications requiring heat resistance.
- Exceptional Strength: The tensile strength and rigidity of Ultem are superior to many competing materials, ensuring lasting performance.
- Chemical Resistance: It withstands exposure to various chemicals and solvents, which is crucial in industrial settings.
- Low Density: The lightweight nature of Ultem makes it suitable for applications where weight reduction is essential.
- Electrical Insulation: Its excellent electrical insulating properties make it a preferred choice in electronics applications.
The Role of Ultem in 3D Printing
The application of Ultem in 3D printing has opened new horizons for various industries. With the advancement of additive manufacturing technologies, Ultem can now be harnessed to create components that were once thought impossible through traditional manufacturing methods. Here are some key aspects of Ultem in the realm of 3D printing:
1. Additive Manufacturing Techniques
Different 3D printing techniques can effectively utilize Ultem. The most prominent methods include:
- Fused Deposition Modeling (FDM): A popular method for creating 3D objects layer by layer, ideal for prototypes and functional parts made from Ultem.
- Selective Laser Sintering (SLS): This process involves laser technology to fuse powdered Ultem, leading to strong, durable parts without requiring support structures.
- PolyJet Printing: This technique allows for multi-material printing, enabling intricate designs with varying properties all in one run.
2. Applications Across Industries
The adaptability of Ultem allows for its use in various sectors, including:
- Aerospace: Parts manufactured from Ultem are lightweight yet durable, making them suitable for aircraft components, helping reduce fuel consumption.
- Automotive: With a growing need for lightweight materials to improve efficiency, Ultem is used for components such as housings, connectors, and interior parts.
- Medical Devices: The excellent biocompatibility and sterilization capabilities of Ultem make it ideal for producing surgical instruments and other medical applications.
- Electronics:Ultem is widely used in the production of insulators, connectors, and circuit boards due to its electrical insulation properties.
Benefits of Using Ultem in 3D Printing
Utilizing Ultem in your 3D printing processes offers several advantages that can significantly enhance your production capabilities:
1. Cost Efficiency
While Ultem may have a higher raw material cost compared to standard thermoplastics, its durability and performance often lead to lower overall costs due to reduced waste and increased lifespan of printed components. Furthermore, 3D printing with Ultem reduces the need for tooling and machining, streamlining the manufacturing process.
2. Design Flexibility
The capabilities of 3D printing allow for complex geometries and customized designs that would be difficult or impossible to achieve with traditional manufacturing methods. Ultem's strength and thermal properties mean that intricate designs can be realized without compromising performance.
3. Rapid Prototyping
3D printing with Ultem drastically cuts down on the time required to develop prototypes. Designers can quickly produce accurate, functional parts for testing and adjustments, speeding up the iterations and enhancing overall productivity.
Best Practices for 3D Printing with Ultem
To achieve the best results when printing with Ultem, consider the following best practices:
1. Optimize Print Settings
When working with Ultem, it's crucial to fine-tune the printer settings such as temperature, bed adhesion, and layer height to optimize the print quality. A heated bed can help with adhesion during the printing process.
2. Post-Processing Techniques
Post-processing can enhance the mechanical properties of 3D printed parts. Techniques like annealing can increase the heat resistance and overall structural integrity of Ultem components.
3. Material Storage
Ultem filaments should be stored in a cool, dry place to avoid moisture absorption, which can negatively impact print quality.
The Future of Ultem in 3D Printing
The future of Ultem in 3D printing looks exceptionally bright as technology continues to advance. With increasing demands for lightweight, robust, and heat-resistant materials, Ultem is poised to become even more prominent in various applications. Innovations in printing techniques and material formulations will likely lead to new possibilities, including:
- Enhanced Customization: Greater capabilities in 3D printing will allow for more tailored applications of Ultem, addressing specific industry challenges.
- Sustainability: As industries lean toward greener practices, research into bio-based Ultem variants may lead to more ecologically friendly production processes.
- Expansion of Use Cases: Emerging sectors, such as robotics and personalized healthcare devices, may discover innovative applications for Ultem due to its unique properties.
Conclusion
In summary, the incredible properties of Ultem and its diverse applications in 3D printing make it a material of choice for engineers and designers alike. Whether you are in the aerospace, automotive, medical, or electronics fields, integrating Ultem into your manufacturing processes can lead to innovative solutions and a stronger competitive edge. As the landscape of 3D printing continues to evolve, Ultem is set to remain pivotal in driving forward new perspectives in design and production.
For more insights on how Ultem and 3D printing can benefit your business, visit Infotron today!